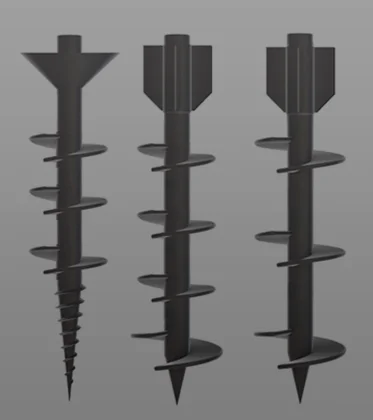
Последнее обновление 16.01.2025
Технические характеристики винтовых свай
Статья расскажет об основных технических характеристиках винтовых свай.
Содержание
Практически все параметры винтовых свай (конструктивные, геометрические) назначаются
индивидуально на основании комплекса данных, но прежде всего на основании информации о
грунтовых условиях в пятне застройки.
Параметр | Основания для назначения |
Марка стали |
Требования к жесткости и прочности; грунтовые условия (в том числе данные о
коррозионной агрессивности грунтов (КАГ); условия эксплуатации.
|
Толщина стенки ствола сваи, мм |
Данные о КАГ; требования к жесткости, прочности.
|
Диаметр ствола сваи, мм |
Данные о КАГ; требования к жесткости, прочности, устойчивости.
|
Длина сваи, мм |
Показатели расчетной глубины промерзания; несущая способность основания.
|
Диаметр лопасти, мм, количество лопастей |
Данные о нагрузках от строения (в соответствии с требованиями к устойчивости);
несущая способность основания.
|
Конфигурация лопасти |
Данные о физико-механических свойствах грунтов: пористость, степень насыщения
водой, консистенция, гранулометрический состав и др.
|
Чтобы получить данные, достаточные для разработки проекта фундамента, совсем не обязательно
заказывать дорогие инженерно-геологические изыскания. Можно воспользоваться
скоростными процедурами, разработанными специалистами ГК
«ГлавФундамент» для объектов малоэтажного строительства:
- геотехнические и геолого-литологические исследования (методика разработана на основании ГОСТ 19912 «Грунты. Методы полевых испытаний статическим и динамическим зондированием»);
- измерения коррозионной агрессивности грунтов.
Количество лопастей

В работе однолопастных конструкций не учитывается трение по боковой поверхности ствола, а
сваи малых длин и диаметров вовсе требуют обязательного применения элемента сопротивления
боковым нагрузкам (ЭСБН) или бетонирования основания колонны, так как крайне неустойчивы к
горизонтальным нагрузкам.
Многолопастные модификации благодаря особенностям конструкции обеспечивают совместную работу
сваи и околосвайного грунта, что позволяет им одинаково хорошо воспринимать вдавливающие и
выдергивающие нагрузки. Подходят для установки в любые, даже слабые, грунты. При нормируемых
осадках не «уходят в срыв».
Конструктивные параметры многолопастных свай (диаметр лопастей, их шаг и соотношение) –
величины, которые находятся в сложной зависимости от характеристик грунтовой среды и
характера нагрузок от сооружения. Если ввести дополнительную без предварительных расчетов,
многолопастная модификация может работать на горизонтальные нагрузки даже хуже, чем
однолопастная дезаксиальная (подробнее).
Увеличение количество лопастей позволяет использовать для ствола трубу меньшего диаметра, но
с большей толщиной стенки (для соблюдения требований к жесткости и прочности).
Ширина лопасти(-ей)
Широколопастные
диаметр лопасти(-ей) в полтора раза и более превосходит диаметр ствола
Узколопастные
диаметр лопасти превосходит диаметр ствола менее чем в полтора раза
Различия в ширине
лопасти
Использование свай с разной шириной лопасти позволяет решить разные задачи:
- осуществить погружение в особо плотные сезоннопромерзающие или многолетнемерзлые грунты с минимальным риском деформации лопасти;
- обеспечить способность к восприятию нагрузок в дисперсных грунтах, в том числе характеризующихся низкой несущей способностью, благодаря достаточной площади опирания.
Вид и конфигурация
лопасти(-ей)
В зависимости от вида лопастей сваи подразделяются:
01
Свая
винтовая лопастная (CBЛ)
Винтовая свая, имеющая одну или несколько
лопастей и ствол со значительно меньшей по
сравнению с лопастью (лопастями) площадью
поперечного сечения; лопасти могут быть
размещены на наконечнике и по длине ствола.
02
Свая
винтовая спиральная (СВС)
Винтовая свая, состоящая из конусного или
открытого наконечника и ствола с приваренной
многовитковой спиралью (спиралями).
03
Свая
винтовая комбинированная (СВК)
Винтовая свая, имеющая конусный или открытый
наконечник с приваренной многовитковой
спиралью и ствол с одной или несколькими
винтовыми лопастями.
Важная характеристика
лопастей широколопастных модификаций – конфигурация. Ее соответствие
грунтовым условиям площадки строительства позволяет установить сваю с минимальным нарушением структуры грунта.
Способ изготовления наконечника
(литье/сварка)
Наконечники свай свариваются (сварные) или отливаются целиком и навариваются на трубу
(литые).
Контакт двух разнородных металлов (металла трубы и металла отливки), характерный для свай с
литыми наконечниками, ведет к образованию гальванической пары, что повышает вероятность
развития коррозии. Кроме того, сварка разнородных металлов – это технологически более
сложный процесс, поэтому стоит обратить особое внимание и на качество сварного шва.
Также запас прочности литого наконечника несопоставимо выше запаса прочности трубы, конечно
(а срок службы конструкции будет определяться по минимальному показателю), если не выбран
ствол, соответствующий ему по толщине (встречается крайне редко, так как цена сваи в этом
случае значительно увеличивается).
Так как формы отливок унифицированы, и изготовить литой наконечник с определенной
конфигурацией лопасти невозможно, сваи со сварным наконечником и лопастью, подобранной
исходя из грунтовых условий, всегда будут иметь большую несущую способность (подробнее).
Толщина стенки ствола
до 3,5 мм
сваи малых толщин
от 4 до 6 мм
сваи средних толщин
6 мм и более
толстостенные сваи
Первая группа рекомендована для строительства легких зданий и сооружений (беседки,
ограждения и т.п.), которые относятся к классу ответственности III (пониженный), при условии
их эксплуатации в неагрессивных грунтовых условиях.
Вторая группа применяется для строений, передающих на фундамент среднюю нагрузку (класс
ответственности III (пониженный), а также для построек II (нормального) класса
ответственности, но только на участках, представленных неагрессивными грунтами.
При строительстве в средне- и сильноагрессивных грунтах и/или при больших нагрузках (классы
ответственности II (нормальный) и I (повышенный)) лучше использовать толстостенные винтовые
сваи.
После выполнения расчета срока службы остаточная толщина стенки обязательно проверяется на
соответствие проектным нагрузкам и требованиям ГОСТ 27751 «Надежность строительных
конструкций и оснований. Основные положения».
Толщина лопасти(-ей)
Толщина лопасти (-ей) может составлять:
- до 5 мм включительно (походят для строительства легких зданий/сооружений, а также временных объектов);
- 6 мм и более (подходят для долговременных построек, крупных гражданских и промышленных объектов, а также для агрессивных грунтовых условий).
Марка стали
При изготовлении винтовых свай используются стали марок:
- Ст3;
- Ст20;
- 09Г2С;
- 30 ХМА.
Подробнее – «На что влияет марка стали?».
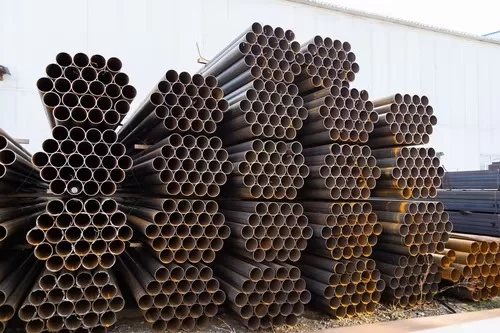
Покрытие
Дополнительная мера защиты от коррозии, так как из-за значительного абразивного воздействия
на сваю в процессе погружения, покрытие почти всегда повреждается.
Подробные результаты испытаний разных покрытий винтовых свай приведены в статье.
Технические характеристики винтовых свай с диаметром
ствола 57, 76, 89, 108, 133, 159, 219, 325 мм
Винтовая свая 57 мм
Конструктивные/геометрические параметры | Часто используемые величины |
Толщина стенки ствола | 3-6 мм |
Ширина/количество витков лопасти (для узколопастных конструкций) | 5-15 мм / 2-5 |
Диаметр/толщина (для широколопастных модификаций) | 120-200 мм / 4-5 мм |
Длина | 2 100-4 500 мм |
При изготовлении, как правило, используется сталь Ст3, Ст20.
Винтовая свая 73, 76 мм
Конструктивные/геометрические параметры | Часто используемые величины |
Толщина стенки ствола | 3-8 мм |
Ширина/количество витков лопасти (для узколопастных конструкций) | 5-15 мм / 2-5 |
Диаметр/толщина (для широколопастных модификаций) | 120-300 мм / 4-6 мм |
Длина | 2 100-5 000 мм |
При изготовлении, как правило, используется сталь Ст3, Ст20.
Винтовая свая 89 мм
Конструктивные/геометрические параметры | Часто используемые величины |
Толщина стенки ствола | 3-9 мм |
Ширина/количество витков лопасти (для узколопастных конструкций) | 5-20 мм / 2-5 |
Диаметр/толщина (для широколопастных модификаций) | 200-360 мм / 4-8 мм |
Длина | 2 600-5 500 мм |
При изготовлении, как правило, используется сталь Ст3, Ст20, 30 ХМА.
Винтовая свая 102, 108 мм
Конструктивные/геометрические параметры | Часто используемые величины |
Толщина стенки ствола | 3,5-8 мм |
Ширина/количество витков лопасти (для узколопастных конструкций) | 5-25 мм / 2-5 |
Диаметр/толщина (для широколопастных модификаций) | 200-460 мм / 6-10 мм |
Длина | 2 600-6 000 мм |
При изготовлении, как правило, используется сталь Ст3, Ст20, 30 ХМА.
Винтовая свая 133 мм
Конструктивные/геометрические параметры | Часто используемые величины |
Толщина стенки ствола | 4-8 мм |
Ширина/количество витков лопасти (для узколопастных конструкций) | 5-30 мм / 2-5 |
Диаметр/толщина (для широколопастных модификаций) | 300-540 мм / 6-10 мм |
Длина | 3 100-7 000 мм |
При изготовлении, как правило, используется сталь Ст3, Ст20, 09Г2С.
Винтовая свая 159, 168 мм
Конструктивные/геометрические параметры | Часто используемые величины |
Толщина стенки ствола | 4,5-8 мм |
Ширина/количество витков лопасти (для узколопастных конструкций) | 10-30 мм / 2-5 |
Диаметр/толщина (для широколопастных модификаций) | 300-650 мм / 6-10 мм |
Длина | 3 600-8 000 мм |
При изготовлении, как правило, используется сталь Ст20, 09Г2С.
Винтовая свая 219 мм
Конструктивные/геометрические параметры | Часто используемые величины |
Толщина стенки ствола | 5-12 мм |
Ширина/количество витков лопасти (для узколопастных конструкций) | 20-30 мм / 2-6 |
Диаметр/толщина (для широколопастных модификаций) | 400-800 мм / 6-10 мм |
Длина | 4 000-12 000 мм |
При изготовлении, как правило, используется сталь Ст20, 09Г2С.
Винтовая свая 273, 325 мм
Конструктивные/геометрические параметры | Часто используемые величины |
Толщина стенки ствола | 6-12 мм |
Ширина/количество витков лопасти (для узколопастных конструкций) | 20-30 мм / 2-6 |
Диаметр/толщина (для широколопастных модификаций) | 500-850 мм / 8-12 мм |
Длина | 4 000-12 000 мм |
При изготовлении, как правило, используется сталь Ст20, 09Г2С.
Автор статьи:
Хабиров Ришат Мавлитянович, Стрижкова Елена Александровна